Камень — гранит, известняк, мрамор, диабаз, базальт — издавна служит человеку в качестве строительного материала. Что же навеяло людям мысль плавить камень? Какие качества отличают плавленый камень?
Плавленый камень по кислотостойкости не уступает фарфору. Даже в кипящих кислотах, которые в течение нескольких часов, а иногда даже минут растворяют любые металлы, каменное литье не разрушается. Устойчивость против истирания у плавленого камня значительно выше, чем у металлов, материал не подвержен «старению», ему незнакома «усталость». Нипочем и трескучие морозы. А будучи отлитым центробежным способом, он имеет еще более высокие показатели.
К преимуществам плавленого камня можно отнести и простоту технологии его получения. Черпай породу ковшом экскаватора, грузи и подвози к печам. Немаловажное значение приобретает и тот факт, что для получения любого металла приходится перерабатывать значительно больше «руды», чем выходит из нее металла. При переработке камня отходы составляют не более десяти процентов.
К сожалению, он хрупок. Но прочность повышается, если его армировать металлом. Кроме того, плавленый камень чувствителен к резким температурным перепадам. Допустимые в настоящее время нормы в жидкой среде — 100, в воздушной — 250 градусов. Ведутся работы по получению термостойких видов литья. Уже имеются составы, способные выдержать температурные перепады в 500 и даже в 600 градусов.
Даже при отсутствии дефицита на металл применение каменного литья будет просто необходимо. Вот один из бесчисленных примеров. Производство таких удобрений, как суперфосфат, раньше сильно беспокоило специалистов. Металлические лопасти мешалок недолго выдерживали влияние агрессивной среды. А те же лопасти из плавленого камня оказались чуть ли не в двадцать раз прочнее. Вообще каменное литье наибольшим спросом пользуется именно у химиков. И не без основания. Оно сберегает тысячи тонн остродефицитного свинца, значительно увеличивает срок службы оборудования. Так, на Кузнецком металлургическом комбинате травильные ванны, облицованные плиткой из каменного литья, служат шесть лет, тогда как свинцовая футеровка менялась через шесть месяцев.
Замена металлических труб трубами из каменного литья также дает значительный экономический эффект. На Криворожском горнообогатительном комбинате металлический трубопровод для транспортировки руды служил самое большое шесть месяцев, а трубы из плавленого камня — в восемь раз дольше. Чугунные лотки гидрозолоудаления на тепловых электростанциях выходят из строя за 9-12 месяцев. А камнелитные трубы могут служить и 20, и 30 лет.
RenegadePizzaGuy
Можно ли «переработать» камень путем его плавления и охлаждения? [закрыто]
Это то, о чем я думал некоторое время.
Скажем, мраморный блок используется для лепки статуи. Большая часть камня откололась и практически бесполезна. Вместо того, чтобы бросить его, возможно, он снова расплавится на кирпичи?
Я спрашиваю об этом, потому что это, вероятно, потребует много энергии и тепла. Я также не уверен, что процесс плавления и охлаждения изменит материал, например сделает его более хрупким.
Изменить: чтобы уточнить, я не имею в виду мрамор конкретно. Я хочу знать, что обычно требуется для расплавления камня, если процесс охлаждения повлияет на него и будет ли это вообще практично делать
Raditz_35
Вы спрашиваете, можно ли расплавить камень и охладить его снова, спрашиваете ли вы конкретно о мраморе, спрашиваете, имеет ли это экономический смысл, спрашиваете, полезно ли это для окружающей среды, спрашиваете, как создаются некоторые виды камней? геологически? Я могу придумать еще дюжину интерпретаций для вашего вопроса, может быть, вы должны быть более конкретными
Эндрю Доддс
Мрамор, являющийся карбонатом кальция, является единственным примером, который НЕ будет работать..
AlexP
Скалы чипсы тоже полезны. И нет никаких экономических причин для переработки камня - в конце концов, Земля - это огромный кусок камня... С другой стороны, переработка камня - это именно то, что делает цикл камня ; это займет очень много времени.
@AlexP Стекло изготовлено из материала, который в изобилии в земной коре; все же мы перерабатываем это.
AlexP
@Kaz: "Сделано из"! = "Есть". Поваренная соль сделана из хлора (ядовитый газ) и натрия (металл, который бурно реагирует с водой). Чтобы сделать стекло из песка, мы тратим огромное количество энергии; имеет смысл избегать этого снова и снова, когда мы можем повторно использовать стекло.
Ответы
Эндрю Доддс
Это зависит от вашего камня.
Такие породы, как гранит , с большими размерами кристаллов, являются результатом ОЧЕНЬ медленного охлаждения и кристаллизации. Таким образом, хотя в теории вы могли бы переплавить и перекристаллизовать этот тип камня, вам, вероятно, потребуются сотни или тысячи лет, чтобы сделать это.
Базальт , мелкозернистая магматическая порода, будет в порядке. Это все еще потребовало бы довольно долгого времени успокоения.
Обсидиановое и вулканическое стекло было бы очень легко - по определению, оно быстро остывает при извержении. Нет проблем с утилизацией, кроме необходимого тепла.
Теперь проблемы..
Песчаник (и другие осадочные породы) - вы не могли расплавить их и переформировать их, очевидно. Вы можете перемолоть их до песчинок, ПОТОМ попытайтесь спрессовать их вместе с соответствующим цементом (кремнезем или карбонат, в зависимости от исходного камня). Это займет давление и совсем немного времени.
Сланец Теперь, вы не только должны размолоть это, но также слегка перекристаллизовать это под давлением на несколько сотен градусов, с большим давлением в направлении, нормальном к расщеплению. В течение долгого времени.
Мрамор Мрамор нельзя плавить при поверхностном давлении, он разлагается на оксид кальция и CO2. Если у вас был тигель очень высокого давления и средство для его нагрева, вы могли бы расплавить мрамор и перекристаллизовать его.
Blueschist Это становится немного сложнее . Вам нужно давление, эквивалентное примерно 20 км породы, и температура около 400 градусов по Цельсию.
Эклогит Тип метаморфической породы очень высокого качества. 45 км глубины и c. 700 градусов С. В течение многих лет, чтобы получить размер кристалла.
Так что... если только вы не хотите, чтобы с ними работали вулканические очки, вероятно, было бы намного проще просто купить еще немного. Формирование скал занимает много времени, и обычно в условиях высокой температуры и давления, которые недешевы для воспроизводства.
kingledion
Отличный ответ. Вы должны указать на общую разницу между магматическими породами (для которых плавление будет работать по определению, хотя, как вы упомянули, время охлаждения варьируется) и другими типами скал.
выраженный в числах
Не могли бы вы добавить оценку, как долго "долго"? В настоящее время я не знаю, если это месяцы и, следовательно, не являются коммерчески жизнеспособными, или мы говорим веками, где мы, скорее всего, не доживем, чтобы увидеть результат.
MSalters
@nwp: Учитывая, что в ближайшее время у нас точно не кончатся скалы, даже один час не будет коммерчески жизнеспособным. Мрамор был бы главным исключением, и это не совсем камень.
PlasmaHH
Для многих камней эти процессы могут давать схожие по составу и физическим качествам, но не по внешнему виду. Специально для мрамора полосы примесей делают его таким красивым, что потребуется еще один дополнительный шаг, чтобы их вставить.
Эндрю Доддс
@nwp - Это зависит, главным образом, от размера кристалла, а следовательно, и от неопределенности. Самые большие кристаллы могут образовываться годами, тысячи лет, в зависимости от того, сколько времени требуется гранитам для охлаждения.
Willk
Здесь есть возможность связать мой самый любимый эпизод «Как это сделано: Изоляция из каменной ваты» . Это точно расплавленная и переработанная порода, которая делается коммерчески.
Идея была навеяна «волосами Пеле», которые действительно существуют на Гавайях: расплавленный базальт, взбитый в тонкие, похожие на волосы пряди. В видео они показывают изготовление искусственной лавы из измельченного базальта (и шлака), которую затем взбивают в шерсть и превращают в маты. Качественный товар.
Тем не менее, большинство камней будет плавиться при температуре около 1500 градусов по Цельсию (2750 по Фаренгейту), предыдущая компания заявляет, что они делают это при температуре 1520º C. Поэтому это довольно сложно и требует передовых технологий.
POJO-парень
Железо плавится при 1538 ° С. Поскольку чугун использовался в кухонной посуде не менее двух тысяч лет, практика плавления и охлаждения достаточно больших количеств материалов при этой температуре не может считаться «высокотехнологичной» - это может относиться к позднему веку железа.
Альберто Ягос
Чугун плавится при 1200ºC. Доменные печи в Европе не появлялись до 13 века.
POJO-парень
Спасибо за исправление. Чугун имеет более низкую температуру плавления, чем чистое железо. 13-й век для доменной печи - это технология позднего средневековья и раннего ренессанса, поэтому она по-прежнему не считается передовой технологией.
ruakh
@ pojo-guy: «Передовые технологии» не обязательно означают то, что вы думаете; В Google легко найти примеры, в которых используются такие термины, как «металлообработка», «гончарное дело», «астрономия», «судостроение», «катание на лошадях» и «колесо». (Я на самом деле не совсем понимаю, что это значит; я не думаю, что это совершенно бессмысленная фраза, но она все еще, вероятно, слишком расплывчата, чтобы быть ужасно полезной в этом ответе.)
ChrisW
Говоря о мраморе, да - исторически люди кормили старый архитектурный мрамор (например, древнеримский мрамор) в печи для извести: чтобы сделать раствор и бетон («известь» является ключевым компонентом в цементе, строительном растворе, бетоне)
Подача мрамора в печи
Почему население начало кормить скульптурные и архитектурные элементы из мрамора, которые, как и везде, когда-то украшали общественные памятники и элитные особняки в Галилее, в соседние ликини? Основная причина, приведенная учеными для такого повторного использования мрамора, заключается в том, что это произошло по экономическим причинам. Как упоминалось ранее, мрамор превосходит известняк, когда речь идет о производстве извести. Хотя это так, для большей части древности мрамор считался слишком редким и ценным товаром, чтобы использоваться для этой цели, и вместо этого использовался, главным образом, в целях украшения и щедрой демонстрации. Когда к поздней античности начали строить ликиновые печи в черте города, ученые пришли к выводу, что это было потому, что к тому времени мрамор был достаточно доступен в виде архитектурных украшений и скульптур. Помимо превосходного качества мрамора, повторное использование этого камня из бывших городских сооружений также, вероятно, позволило сэкономить значительные транспортные расходы. Тогда, по мнению этих ученых, сжигание скульптурного и архитектурного мрамора в известковых печах, установленных в городах во время поздней античности, было в первую очередь выбрано из-за его производительной эффективности: продукт был превосходнее, а транспортировка более рентабельной.
Так что для этого особого типа "рока" не нужны очень продвинутые технологии... они делали это в реальном мире, в древности.
Draco18s
Это не совсем ответ на вопрос. Вопрос состоит в том, чтобы узнать, могут ли они сделать камень из обрывков породы, расплавив и растворив его (на примере мрамора), чтобы получить новый материал для лепки. Это ответ на вопрос о том, можно ли специально использовать металлолом для другого промышленного использования, кроме скульптуры.
ChrisW
ОП спросил, можно ли мрамор превратить в кирпичи. Другие ответы предположили, что это сложно; в то время как этот ответ предполагает, что нечто подобное было сделано в реальном мире с использованием старинных технологий, так что, возможно, этот ответ действительно что-то добавляет и стоил того.
Великая утка
Это не в состоянии ответить на вопрос. ОП хочет знать, можно ли расплавить мрамор и превратить его в мрамор.
Дэвид Ричерби
@ChrisW Нет, он превращает каменную крошку в состав раствора: кирпичи сделаны из глины. И я прокомментировал как прямой ответ на ваш комментарий. (Кроме того, мне нравится, что люди, которые понижают голос без объяснения причин, получают комментарии «Даунвотер, пожалуйста, объясните», в то время как те, кто объясняют, получают удар словами «Ну, вы могли бы просто понизить голос».)
ivanivan
Есть, конечно, и другие способы повторного использования, неиспользования или перепрофилирования вещей.
Осколки можно очень тонко измельчать / измельчать, а затем использовать для смешивания с каким-либо другим веществом для придания прочности (например, для изготовления цемента или для изготовления металлических опилок в чем-то вроде JB Weld) или для изготовления других изделий (наждачная бумага очень хороша) молотый камень / минерал различных типов, приклеенный к бумаге)
И, конечно же, всегда можно использовать только небольшие куски каменно-дренажных систем, как часть большого фильтра для естественной воды, мощения и т. Д.
Тем не менее, в относительно небольших масштабах - как и те остатки, которые были после того, как Микеланджело вырезал своего Дэвида, - он не предоставил бы достаточно значительных остатков для экономии масштаба, чтобы сделать что-то и сделать что-либо, но оставить большие куски для небольших работ. или тренировка, и т. д. или бросание небольших кусков во французскую канализацию.
Мартин Боннер
На самом деле, в случае мрамора, я подозреваю, что отходы Микеланджело были бы сожжены для извести - мрамор делает высококачественную негашеную известь, но обычно для этого слишком ценна.
Все знают, что извержение вулкана — это страшное природное явление. Лава уносит тысячи людей, поглощает все живое, превращая в пепел. Убежать от нее практически нереально. Плавление камня позволяет получить лаву и в домашних условиях!
youtubeПоэтому не рекомендуется строить жилье вблизи вулканов. Даже если они потухшие, в любой момент могут ожить и тогда беде не миновать. Но люди не смотрят на предупреждения гидрометцентров и продолжают застраивать пустые места.
Лава — раскалённая масса, вязкая на вид, которая появляется из камней силикатного состава под воздействием огромных температур и извергается из вулканов.
Канал King of Random решил показать своим подписчикам, как можно в домашних условиях превратить обычные камни в лаву. Для этих целей они использовали плавильню и последние технологии.
Ребятам из канала поступило письмо. Они по заслуге оценили идею и решили ее воплотить в жизнь. Короли рандома не боятся трудностей и готовы принять любой вызов.
Король рандома предложил два способа превратить камни в лаву. Первый способ заключался в том, чтобы нагреть натуральный материал в печи, а второй — разогреть камень при помощи внешнего воздействия специального приспособления, напоминающего сварочный аппарат.
В результате первого способа, камни расплавились, но быстро стали твёрдыми и хрупкими. А вот при втором способе ребятам удалось добиться желаемого результата. Температура плавления камней различна. Она зависит от их химической природы.
Смотрите интересное и познавательное видео! Такого вы точно нигде и никогда ещё не видели! Захватывающий ролик. Приятного просмотра и хорошего дня!
Камень — гранит, известняк, мрамор, диабаз, базальт — издавна служит человеку в качестве строительного материала. Что же навеяло людям мысль плавить камень? Какие качества отличают плавленый камень?
Плавленый камень по кислотостойкости не уступает фарфору. Даже в кипящих кислотах, которые в течение нескольких часов, а иногда даже минут растворяют любые металлы, каменное литье не разрушается. Устойчивость против истирания у плавленого камня значительно выше, чем у металлов, материал не подвержен «старению9raquo;, ему незнакома «усталость9raquo;. Нипочем и трескучие морозы. А будучи отлитым центробежным способом, он имеет еще более высокие показатели.
К преимуществам плавленого камня можно отнести и простоту технологии его получения. Черпай породу ковшом экскаватора, грузи и подвози к печам. Немаловажное значение приобретает и тот факт, что для получения любого металла приходится перерабатывать значительно больше «руды9raquo;, чем выходит из нее металла. При переработке камня отходы составляют не более десяти процентов.
К сожалению, он хрупок. Но прочность повышается, если его армировать металлом. Кроме того, плавленый камень чувствителен к резким температурным перепадам. Допустимые в настоящее время нормы в жидкой среде — 100, в воздушной — 250 градусов. Ведутся работы по получению термостойких видов литья. Уже имеются составы, способные выдержать температурные перепады в 500 и даже в 600 градусов.
Даже при отсутствии дефицита на металл применение каменного литья будет просто необходимо. Вот один из бесчисленных примеров. Производство таких удобрений, как суперфосфат, раньше сильно беспокоило специалистов. Металлические лопасти мешалок недолго выдерживали влияние агрессивной среды. А те же лопасти из плавленого камня оказались чуть ли не в двадцать раз прочнее. Вообще каменное литье наибольшим спросом пользуется именно у химиков. И не без основания. Оно сберегает тысячи тонн остродефицитного свинца, значительно увеличивает срок службы оборудования. Так, на Кузнецком металлургическом комбинате травильные ванны, облицованные плиткой из каменного литья, служат шесть лет, тогда как свинцовая футеровка менялась через шесть месяцев.
Замена металлических труб трубами из каменного литья также дает значительный экономический эффект. На Криворожском горнообогатительном комбинате металлический трубопровод для транспортировки руды служил самое большое шесть месяцев, а трубы из плавленого камня — в восемь раз дольше. Чугунные лотки гидрозолоудаления на тепловых электростанциях выходят из строя за 9-12 месяцев. А камнелитные трубы могут служить и 20, и 30 лет.
1975 ЦК ВЛКСМ Изд. «Молодая гвардия»
2009 «Эврика!9raquo;
16. Производство металлов. Когда плавится камень?
Вот тебе и нынешнее воспитание, - назидательно произнес Янечек. - А если иной раз скажешь что-нибудь сыну, отвечает: «Вы, батя, этого не понимаете, теперь другие времена, другая эпоха… Ведь и костяное оружие, говорит, еще не последнее слово: когда-нибудь материал». Ну, знаешь ли, это уж слишком: разве видел кто материал крепче камня, дерева или кости! Ты хоть и глупая баба, а должна признать: что… что… ну, что это переходит все границы.
Карел Чапек. О падении нравов (из сб. «Апокрифы»)
Сейчас мы просто не в состоянии представить нашу жизнь без металлов. Мы привыкли к ним настолько, что по крайней мере подсознательно противимся - и в этом подобны процитированному выше герою доисторической эпохи - всяким попыткам заменить металлы чем-нибудь новым, более выгодным. Нам хорошо известно, с каким трудом в некоторых отраслях пробивают себе дорогу более легкие, более долговечные и более дешевые материалы. Привычка - это железный корсет, но и он, будь он из пластика, был бы все-таки более удобным. Впрочем, мы перескочили пару-другую тысячелетий. Первые потребители металла вообще не подозревали, что будущие поколения поставят их открытие в ряд с самыми выдающимися вехами на пути экономического и технического развития - с возникновением земледелия и с промышленной революцией XIX столетия.
Открытие, вероятно, состоялось - как это иногда случается - в результате какой-то неудачной операции. Ну, например, так: доисторическому земледельцу потребовалось пополнить запас каменных пластинок и топоров. Из кучи заготовок, лежавшим у его ног, он выбирал камень за камнем и умелым движениями отбивал одну пластину за другой. А потом в его руки попал какой-то блестящий угловатый камень, от которого, сколько он ни бил по нему, ни одна пластинка не отделялась. Более того, чем усерднее он дубасил по этому бесформенному куску сырья, тем больше тот начинал походить на лепешку, которую в конце концов можно было мять, крутить, вытягивать в длину и свивать в самые удивительные формы. Так люди впервые познакомились со свойствами цветных металлов - меди, золота, серебра, электрона. При изготовлении первых, очень простых украшений, оружия и инструментов им было достаточно самого распространенного технического приема каменного века - удара. Но эти предметы были мягкими, легко ломались и затуплялись. В таком виде они не могли угрожать господству камня. А кроме того, металлы в чистом виде, поддающиеся обработке камнем в холодном состоянии, в природе встречаются крайне редко. И все-таки новый камень им понравился, поэтому они экспериментировали с ним, комбинировали приемы обработки, ставили опыты, думали. Им пришлось, естественно, пережить много неудач, и прошло очень много времени, прежде чем им удалось открыть истину. При высокой температуре (ее последствия они хорошо знали по обжигу керамики) камень (который мы сегодня называем медью) превращался в текучее вещество, принимавшее вид любой формы. Инструменты могли обрести очень острую режущую кромку, которую к тому же можно было затачивать. Сломанный инструмент не надо было выбрасывать - достаточно было его расплавить и снова отлить в форме. Потом они пришли к открытию, что медь можно получать обжиганием различных руд, которые встречаются куда чаще и в большем объеме, нежели чистые металлы. Конечно, они не узнали с первого взгляда металл, скрытый в руде, но эти ископаемые, несомненно, привлекали их своей пестрой окраской. А когда к этому после длинного ряда случайных, а впоследствии сознательных количественных экспериментов прибавилось открытие бронзы - твердого золотистого сплава меди и олова, длившееся миллионы лет господство камня пошатнулось в само своем основании.
В Центральной Европе медные изделия впервые появились в единичных случаях на закате неолита, несколько чаще они встречались в энеолите. Однако уже раньше, в седьмом - пятом тысячелетиях до н. э. более развитый Ближний Восток начал получать медь плавкой пригодных для этой цели окисных (куприт), карбонатных (малахит), а позднее и сульфидный руд (медный колчедан). Самой простой была плавка окисных руд, полученных из выветрелых медных месторождений. Такие руды можно при температуре 700–800 град. восстановить в чистую медь:
Cu2 O + CO U&4; 2Cu+CO2
Когда древние литейщики прибавили к этому продукту олово (вспомним о египетском рецепте), возник сплав, который по своим свойствам далеко превосходил медь. Уже полпроцента олова повышает твердость сплава в четыре раза, 10 процентов - в восемь раз. Одновременно снижается точка плавления бронзы, на пример при 13 процентах олова почти на 300 °C. Отрылись врата в новую эпоху! За ними мы уже не встретим то старое однородное общество, где каждый делал почти все. Изготовлению предмета из металла предшествовал долгий путь - поиски рудных месторождений, добыча руды, плавка в плавильных ямах либо печах, разливка в изложницы; все это требовало целого комплекса специальных знаний и навыков. Поэтому среди ремесленников начинается дифференциация по специальностям: горняки, металлурги, литейщики и, наконец, торговцы, род занятий которых необходим остальным и потому ими высоко ценится. Не каждый мог успешно заниматься всем комплексом столь сложной деятельности. Со многими неудачами и трудностями столкнулись и современные экспериментаторы, когда попытались повторить некоторые технологические приемы доисторических металлургов и литейщиков.
Сергей Семенов обнаружил трассологическим методом и экспериментально подтвердил тот факт, что на заре бронзовой эры люди использовали для добычи и дробления руд весьма грубые каменные орудия из гранита, диорита и диабаза в виде мотыг, дубинок, наковален и дробилок.
Плавку малахитовой руды экспериментаторы опробовали в небольшом углубленном горне без использования воздушного дутья. Горн они высушили и обложили каменными плитами таким образом, что возникла круглая амбразура с внутренним диаметром около одного метра. Из древесного угля, использовавшегося в качестве топлива, в горне сделали конусообразное сооружение, в середину которого положили руду. После нескольких часов горения, когда температура открытого пламени достигала 600–700 °C, малахит расплавился до состояния оксидической меди, то есть металлическая медь не образовалась. Аналогичный результат был достигнут и в следующей попытке, когда вместо малахита использовали куприт. Причина неуспеха заключалась, по всей вероятности, в избытке воздуха в горне. Новый тест с малахитом, накрытым перевернутым керамическим сосудом (весь процесс протекал так же, как и в предыдущих случаях), принес в итоге медь губчатого вида. Небольшое количество цельной меди экспериментаторы получили лишь тогда, когда малахитовую руду перед плавкой раздробили. Сходные опыты были проведены в Австрии, альпийские руды которой имели огромное значение для доисторической Европы. Однако в печь экспериментаторы нагнетали воздух, благодаря чему достигли температуры 1100 °C, которая восстанавливала окислы в металлическую медь.
В одном из опытов экспериментаторы использовали для отливки бронзового серпа сохранившуюся из находок у Цюрихского озера половину оригинальной каменной формы, к которой изготовили парную сторону. Обе части формы высушили при температуре 150 °C и лили бронзу при 1150 °C. Форма осталась неповрежденной, отливка была хорошая. Тогда решили опробовать уже бронзовую двухстворчатую форму для топора, найденную во Франции. Она была тщательно просушена при температуре 150 °C. Потом ее залили бронзой при температуре 1150 °C. Было получено изделие великолепного качества. При этом не было обнаружено ни малейшего повреждения на бронзовой форме, что стало самым важным результатом эксперимента. Дело в том, что перед экспериментом некоторые исследователи высказывали мнение, что горячий металл, по всей вероятности, соединится с материалом формы.
При производстве предметов более сложной конфигурации древние литейщики использовали технику литья с потерей литейной формы. Восковую модель они обмазывали глиной. При обжиге глины воск вытекал, и его потом замещала бронза. Однако, вынимая бронзовую отливку, формы приходилось разбивать, так что рассчитывать на ее вторичное использование не приходилось. Экспериментаторы отрабатывали этот метод, исходя из технологической инструкции XVI века по изготовлению золотых и серебряных бубенчиков. Во время опытов они заменили золото медью, чтобы одновременно проверить возможность замены драгоценных металлов обычными. Температура плавления золота равна 1063 °C, меди - 1083 °C. В качестве образца была выбрана отливка медного бубенчика из стоянки первого тысячелетия до н. э. Форму изготовили из смеси глины и древесного угля, а модель - из пчелиного воска. Малое ядро сделали из смеси глины и молотого древесного угля и поместили в него маленький камешек - сердце бубенчика. Воск нанесли вокруг ядра тонким слоем, равным толщине стенки будущей отливки, и прилепили восковое кольцо, образующее подвесок будущего бубенца. Восковую бобышку в форме рукоятки прикрепили над кольцом таким образом, чтобы она служила бункером для расплавленного металла во время разливки, затвердевания и усадки металла в отливке. В восковой оболочке на нижней части бубенца вырезали отверстие, чтобы формообразующая смесь из глины, древесного угля и воска заполнила отверстие и зафиксировала положение ядра после выплавки восковой модели и во время литья. Обернутую форму в верхней части проткнули несколькими соломинами, которые позже либо сгорели, либо просто были удалены. Через возникшие отверстия из формы во время литья выходил горячий воздух. Всю модель покрыли несколькими слоями размолотой глины и древесного угля и в течение двух дней сушили. Потом ее еще раз покрыли слоем угля и глины (для прочности формы) и над бобышкой прикрепили воронкообразный заливочный бункер из той же формообразующей смеси. Бобышку прикрепили слегка наискось, чтобы форма отливалась в наклонном состоянии. Это должно было обеспечить беспрепятственное стекание расплавленного метла по нижней части ее лицевой стороны, в то время как по противоположной стороне должен был происходить отток вытесняемого металлом воздуха до полного наполнения всей формы расплавленным металлом. Перед плавкой в бункер закрытый крышкой бросили обломки медной руды. После сушки форму поместили в печь, оборудованную каналом, обеспечивающим тягу. Печь заполнили четырьмя с половиной килограммами древесного угля и разогрели до температуры 1200 °C. Восковая модель и восковая бобышка расплавились и выпарились, медь расплавилась и стекла в форму, где и образовала металлический бубенчик. Потом внешнюю «рубашку» разбили, металлическую бобышку удалили, а глиняное ядро, образовавшее полую часть бубенца, выковыряли - остался только камешек.
Артур Питч провел целую серию экспериментов, посвященных чеканке бронзы: выделке проволоки, спирали, листа, сплошного кольца и профильного прута. Приобретенный опыт был использован им при изготовлении реплик бронзовых крученых колец дуринской культуры, относящейся к раннему железному веку. Всего сделал он семнадцать реплик, каждую из которых снабдил описанием археологического оригинала, перечнем использованных инструментов и приспособлений, анализом вещественного состава и, наконец, объяснением отдельных операций и указанием на длительность технологического процесса. Менее всего времени было затрачено на реплику номер два - двенадцать часов. Наибольшее - шестьдесят часов - потребовала реплика номер четырнадцать.
На протяжении бронзового века стали постепенно выявляться и неудобства, связанные с производством, прежде всего ограниченное наличие в природе сырьевых источников и истощение известных к тому времени месторождений. Это, безусловно, было одной из причин, почему люди искали новый металл, который мог бы удовлетворить постоянно возрастающие потребности. Этим требованиям отвечало железо. Сначала судьба его напоминала судьбу меди. Первое железо, метеоритного происхождения, либо полученное случайно, появилось уже в третьем и втором тысячелетиях до н. э. в Восточном Средиземноморье. Более трех тысячелетий назад стали работать металлургические печи в Передней Азии, Анатолии и Греции. У нас они появились в гальштатскую эпоху, но окончательно привились только в латенскую эпоху.
Среди сырья, применявшегося в древнем железоплавильном деле (окислы, карбонаты, силикаты). Наиболее распространенными были окислы: гематит, или железный блеск, лимонит, или бурый железняк, - смесь гидроокисей железа и с большим трудом восстанавливаемый магнетит.
Восстановление железа начинается уже приблизительно при температуре 500 °C. Вы, вероятно, сейчас зададите вопрос, почему железо стало применяться на столетия или тысячелетия позже меди и бронзы. Это объясняется условиями его тогдашнего производства. При тех температурах, которые достигались первыми металлургами в их горнах и печах (около 1100 °C), железо никогда не переходило в жидкое состояние (для этого необходимо хотя бы 1500 °C), а скапливалось в виде тестообразной массы, которая в благоприятных условиях сваривалась в крицу, пропитанную шлаком и остатками горючих материалов. При такой технологии в железо из древесного угля переходило ничтожно малое количество углерода - около одного процента, поэтому оно было мягким и поддающимся ковке даже в холодном состоянии. Изделия из такого железа не достигали твердости бронзы. Острия легко загибались и быстро затуплялись. Это было так называемое прямое, непосредственное производство железа. Оно сохранялось вплоть до XVII столетия. Правда, в некоторых доисторических и раннесредневековых печах можно было получить железо с более высоким уровнем углеродистости, то есть некое подобие стали. Только с XVII столетия стали применяться печи, где железо производилось в жидком состоянии и с высоким содержанием углерода, то есть твердое и хрупкое, из которого отливался слиток. Для получения стали необходимо было высокоуглеродистому железу придать ковкость путем удаления части содержащегося углерода. Поэтому такой метод называется непрямым производством железа. Но и доисторические кузнецы путем экспериментов расширяли свой опыт. Они обнаружили, что, нагревая железо в кузнечном горне, когда температура от древесного угля достигнет 800–900 °C, можно получать изделия с гораздо лучшими свойствами. Дело в том, что на их поверхности образуется тонкий слой с более высоким содержанием углерода, который придает предмету качества низкоуглеродной стали. Твердость железа возросла, когда был открыт принцип закалки и стали использоваться его преимущества.
Вероятно, самый ранний эксперимент в изучении древней металлургии распорядился провести около ста лет назад граф Вурмбранд. Его рабочие-металлурги в простейшем горне диаметром полтора метра использовали древесный уголь, обожженную руду и в процессе плавки улучшали условия горения слабым нагнетанием воздуха. Через двадцать шесть часов они получили приблизительно двадцатипроцентный выход железа, из которого выковали различные предметы. Сравнительно недавно плавку железной руды в аналогичном устройстве провели и английские экспериментаторы. Простой плавильный горн они реконструировали по подобию горна, обнаруженного на одной древнеримской стоянке. Оригинальный горн имел диаметр 120 см и глубину 45 см. Перед плавкой английские исследователи обожгли руду в окислительной среде при температуре 800 °C. После зажигания древесного угля в горн постепенно добавляли новые слои руды и древесного угля. В ходе эксперимента было использовано искусственное дутье фурмой. Для того, чтобы один слой руды, восстановленный окисью углерода, проник в под, требовалось около четырех часов. Рабочая температура доходила до 1100 °C, и железо скапливалось около устья фурмы. Выход в процессе плавки составил 20 процентов. Из 1,8 кг руды было получено 0,34 кг железа.
Опыты Гиллеса в 1957 году открыли серию экспериментов, посвященных восстановлению руды в различных типах шахтных печей. Уже в первых опытах Иозеф Вильгельм Гиллес доказал, что доисторическая печь шахтной конструкции могла успешно работать, используя естественное движение воздуха на подветренных склонах. Во время одного из тестов он зафиксировал в центре печи температуру от 1280 до 1420 °C, а в пространстве колосника - 250 °C. Результат плавок - 17,4 кг железа, то есть 11,5 процента: шихта состояла из 152 кг бурого железняка и железного блеска и 207 кг древесного угля.
Множество опытных плавок в репликах печей римской эпохи провели в Дании, особенно в Лейре. Выяснилось, что одна удачная плавка может дать 15 кг железа. Для этого датчане должны были использовать 132 кг болотной руды и 150 кг древесного угля, который получили жжением одного куб. м древесины лиственных пород. Плавка продолжалась около 24 часов.
Систематические эксперименты проводятся в Польше в связи с изучением обширного железоделательного ареала, открытого в Свентокшиских горах. Его расцвет относится к поздней римской эпохе (от третьего до четвертого столетия н. э.). Только с 1955 по 1966 год археологи исследовали в Свентокшиских горах 95 металлургических комплексов с более чем 4 тысячами железоплавильных печей. Археолог Казмеж Беленин полагает, что общее число таких комплексов в этом ареале составляет 4 тысячи с 300 тысячами печей. Объем их продукции мог достигать 4 тысяч тонн железа рыночного качества. Это огромная цифра, не имеющая аналогов в доисторическом мире.
Истоки упомянутого железоплавильного производства восходят к позднему латену (последнее столетие до н. э.) и раннему римскому периоду, когда металлургические комплексы с десятью или двадцатью печами располагались непосредственно в центре населенного пункта. Их продукция удовлетворяла лишь местные, весьма ограниченные потребности. Начиная со среднего римского период производство железа стало носить организованный характер, наибольшего подъема оно достигла в III–IV веках. Печи располагались в виде двух прямоугольных отсеков, разделенных штреком для обслуживающего персонала. В каждом из отсеков печи группировались по две, три и даже по четыре. Таким образом, в одном комплексе размещалось несколько десятков печей, однако не были какими-то редкими исключениями и поселения с сотней и даже двумя сотнями печей. Гипотеза о существовании в этот период экспорта железа подтверждена не только количеством металлургических печей с высокой продуктивностью, но и многочисленными находками кладов с тысячами римских монет. В эпоху Великого переселения народов и в раннем средневековье производство снова упало до уровня, отвечавшего местным потребностям.
Предпосылкой возникновения столь массового металлургического производства в римскую эпоху стали достаточные запасы дерева и руды. Металлурги использовали бурый железняк, гематит, а также железный шпат. Некоторые руды они добывали обычным горняцким способом, о чем свидетельствует, например, шахта Сташиц с системой шахтных стволов, штолен и с остатками крепи и инструментов, относящихся к римской эпохе. Впрочем, не гнушались они и болотной рудой. Применялись печи с углубленным подом и надземным стволом, который при выемке железной губки (крицы) приходилось разбивать.
Начиная с 1956 года в Свентокшиских горах проводят эксперименты, которые реконструируют производственный процесс: добычу руды на кострах (для удаления влаги, обогащения и частичного сжигания вредных примесей, например серы); получение древесного угля углежжением в штабелях; строительство печи и сушку ее стен; разжигание печи и непосредственную плавку; разработку ствола шахты и выемку железной кубки; проковку железной кубки.
В 1960 году на одной из самых известных стоянок (Нова Сбупя) был открыт Музей древней металлургии, неподалеку от которого ежегодно, начиная с 1967 года, в сентябре демонстрируется для широкой публики технология доисторической металлургии. Такая демонстрация начинается с доставки руды из шахты в металлургический комплекс, в котором на разных уровнях размещены железоплавильные печи. Здесь руда размельчается молотами и сушится. Сушка и обогащение руды происходят в обжиговых сооружениях. Такое устройство имеет форму штабеля, образуемого слоями дров, переложенными рудой. Штабель поджигается одновременно со всех сторон. После сгорания высушенную, обожженную и обогащенную руду складывают в кучу, откуда ее берут для загрузки. В окрестностях комплекса находится также рабочее место угольщиков, где показывается производство древесного угля - закладка и возведение штабеля, выжигание, разборка штабеля, транспортировка угля на открытый склад, измельчение и, наконец, использование в печи. Затем следует разогрев печи, монтаж и закладка мехов. Персонал комплекса составляют десять работников - шахтеров, металлургов, угольщиков и подсобных рабочих, которые ведут плавку и одновременно готовят к эксперименту вторую печь. Плавка продолжается выемкой железной губки из пода, причем предварительно шахту не обходимо разбить.
В 1960 году польские и чешские специалисты объединили свои усилия и стали совместно проводить металлургические эксперименты. Они построили две восстановительные печи по образцам римской эпохи. Одна была аналогом типа печи из Свентокшиских гор, вторая соответствовала археологической находке в Лоденицах (Чехия). Для плавки были использованы гематитовая руда и буковый уголь в пропорции один к полутора и один к одному и слабое воздушное дутье. Систематически контролировали и измеряли приток воздуха, температуру и восстановительные газы. Во время эксперимента на аналоге польской печи, которая имела углубленный под и разные шахтные надстройки - высотой в 13, 27 и 43 см, ученые обнаружили, что плавильный процесс сосредоточился у горловин обеих противоположных фурм, где образовались подвижный шлак и губчатое железо (от 13 до 23 процентнов железа и лишь около одного процета металлического железа в каплях в составе нижнего шлака). Температура вблизи фурм достигала 1220–1240 °C.
Подобным же образом процесс протекал и во время опытов в лоденицкой печи; лиш9ь вид шлаковых и железных образований был иной. Температура вблизи фурмы составляла 1360 °C. И в этой реплике была получена железная крица со следами науглероживания. Железная кубка образовывалась всегда у горловин фурм, в то время как более легкий шлак протекал сквозь ее поры в под на слой древесного угля. Эффективность в обоих случаях не превышала 17–20 процентов.
Дальнейшие опыты были нацелены на выяснение уровня славянского металлургического производства VIII столетия, остатки которого сохранились в комплексах, открытых в Желеховицах у Уничова в Моравии. Речь шла прежде всего о том, чтобы определить, можно ли было в таких печах изготавливать сталь. Что касается выхода железа и эффективности печи, то это представляло второстепенный интерес, ибо проводившиеся в ходе эксперимента многочисленные измерения неблагоприятно влияли на процесс плавки.
Печи желеховицкого типа - замечательные устройства остроумной конструкции. Их форма позволяла проводить качественное наполнение завалкой. Опыты показали, что металлурги при плавке могли изготовлять древесный уголь сами. Топливо нужно было закладывать в печь малыми порциями, в противном случае появлялась опасность заблокировать узкое шахтное отверстие вплотную над подом печи. Бесспорным преимуществом обладали легкоплавкие железные руды, но печи желеховицкого типа были в состоянии восстанавливать и гематиты, и магнетиты. Предварительный обжиг руды не представлял сложности и был, по всей вероятности, в любом случае выгодным. Сантиметровый размер кусков руды был оптимальным.
Завалка образовывала плавящийся конус в поду печи, и засыпавшийся следом материал потом автоматически транспортировался к полости за фурмой, где образовывался эпицентр жала в котором продукт предохранялся от реоксидирования нагнетаемым воздухом.
Важным параметром является объем нагнетаемого в печь воздуха. Если дутье недостаточно, температура слишком низкая. Больший объем воздуха ведет к значительной потере железа, переходящего в шлак. Оптимальный объем вдуваемого воздуха, составлял для желеховицкой печи 250–280 л в минуту.
Далее экспериментаторы обнаружили, что при определенных условиях можно даже в примитивных отдельных печах получить высокоуглеродистую сталь и, следовательно, нет нужды в последующем науглероживании. Во время опытов на желеховицком комплексе археологи отметили тот факт, что все печи снабжены за фурмой раковиной. Это пространство они гипотетически приняли за камеру для нагревания и науглероживания крицы, которая там накапливалась сразу после плавки. Высказанную гипотезу они проверили в реплике желеховицкой печи. После шестичасовой плавки гематитовой руды с угля крицу нагрели в восстановительной среде в задней полости печи. Температура в камере составила 1300 °C. Продукт извлекли из печи при красно-белом калении. Шлак протекал через поры губчатой железной массы. Продукт содержал наряду с чистым железом железо науглероженное.
Во время новгородской археологической экспедиции в 1961 и 1962 годах были проведены экспериментальные плавки железа в реплике древнерусской надземной шахтовой печи X–XIII веков, хорошо известной как по археологическим, так и по этнографическим источникам. Учитывая то обстоятельство, что просушка печи из глины - а именно из нее были сделаны оригиналы - затянулась бы на несколько недель, экспериментаторы использовали при ее изготовлении сырье глиняные блоки. Зазоры между ними заполнили смазкой из глины и песка. Внутренность печей обмазали приблизительно сантиметровым слоем глины с песком. Печь имела цилиндрическую форму диаметром 105 см и высотой 80 см. Шестидесятисантиметровая домница была размещена в центре, цилиндра. Диаметр верхнего отверстия составлял 20 см, пода - 30 см. В нижней части печи экспериментаторы сделали отверстие размером 25х20 см, которое служило для нагнетания воздуха и выпуска шлака. Контроль за режимом внутри печи проводился через два диоптера в стенке, через которые были введены части измерительной аппаратуры. Дутье проводили новейшим способом - электромотором, мощность которого привели в соответствие с параметрами, достигавшимися кузнечными мехами. Двадцатисантиметровая фурма была опять репликой старого типа, изготовленной из смеси глины и песка. Пе6чь сохла три дня при нормальных погодных условиях.
Для плавок использовали по большей части болотную руду с весьма высоким содержанием железа (около 77 процентов), а в двух случаях и гипергенную руду, которую дробили до величины грецкого ореха. Перед завалкой руду высушили, а часть даже около получаса обжигали на огне. Плавка началась с разогрева печи сухими сосновыми поленьями с естественной тягой в течение двух часов. Потом домницу вычистили и под покрыли тонким слоем угольной пыли и колотого угля. Затем последовала установка фурмы и обмазка всех щелей глиной. Дутье начали, когда шахта была полностью заполнена через дымовое отверстие древесным углем. Спустя пять - десять минут сосновый уголь разгорелся, и через полчаса треть его сгорела. Пустое пространство, образовавшееся в верхней части шахты, было заполнено шихтой, состоявшей из угля и руды. Когда шихта осела, в образовавшуюся пустоту добавили еще порцию. Всего было проведено семнадцать опытных плавок.
Из завалки, состоявшей из 7 кг руды и 6 кг древесного угля, получили 1,4 кг губчатого железа (20 процентов) и 2,55 кг шлака (36,5 процентов). Масса древесного угля ни в одной из плавок не превышала массы руды. Плавки, проведенные при повышенных температурах, давали меньший объем железа. Дело в том, что при более высоких температурах в шлак переходило большее количество железа. Серьезное влияние на качество и эффективность плавки оказывала помимо температурного режима точность выбора оптимального момента для выпуска шлака. При слишком раннем либо, наоборот, слишком позднем выпуске шлак поглощал окислы железа, и это вело к меньшему объему выхода продукции. При высоком содержании окислов железа шлак становился вязким и поэтому хуже вытекал и отделался от губчатого железа.
Значение новгородских экспериментов особенно велико потому, что во время некоторых из них удалось выпустить шлак. Плавка длилась от 90 до 120 минут. В этом типе печи можно было за один цикл обработать до 25 кг руды и получить более 5 кг железа. Восстановленное губчатое железо осаждалось не непосредственно на дне печи, а несколько выше. Получение металлического чугуна из этого продукта представляло собой дальнейшую самостоятельную и сложную операцию, связанную с новым нагревом. И эти эксперименты подтвердили гипотезу о том, что и в обычных восстановительных печах при определенных условиях происходит науглероживание железа, то есть получается сырьевая сталь. В восстановительных печах, где процесс протекал без выпуска шлака, был получен конгломерат, которые состоял из губчатого железа (верхней части), шлака (в нижней части) и остатков угля. Отделение губчатого железа от шлака обыкновенно проводилось механическим способом.
В последнее время археологи обнаружили в Моравском Красе, в районе города Бланско, множество следов древней металлургической деятельности - поды печей, обломки, стен, фурм, кусковую породу, - датируемых X столетием. В модели одной из печей с карманообразным подом был проведен эксперимент, который показал, что в таком устройстве также могла производиться науглероженная стал и что губчатое железо спекается на уровне фурмы, и потому его невозможно обнаружить под шлаковыми слитками.
Плавление осадных пород, спекание камня(кальция).
Здравствуйте, мысль такая: у нас есть много камня осадных пород, можно ли его плавить, и потом по принципу 3D принтеров возводить стены зданий из монолитного камня.
Как я понял камень поверхностный в основном состоит из осадных пород мертвых организмов, т.е. кальций. Он должен быть достаточно легкоплавкий 580градусов гугл подсказал, если плавить при такой температуре то большая часть осадных пород будет расплавлена иприобретет пластичную массу как цементный раствор.
Скажите такое можно реализовать, и вообще реальна ли моя затея?
Имеется ввиду наличие бесплатной энергии.
#7 tvv385
Погуглите «петралгия» — старая довольно изрытая тема, аналогично «металлургии».
А почему не делают? А сам удивляюсь — совок же — партия наверно забыла приказать)
#8 химик-философ
химик-философ
Осадная бывает артиллерия, а породы называются осадочными. Осадочные породы не являются легкоплавкими, т.к. основные их компоненты — силикаты, все, как правило тугоплавкие. Осадочнве карбонаты вообще не плавятся, а разлагаются. Плавят базальт и ему подобные породы, но температура плавления их начинается с 900°С.
Как бы базальт тоже силикат.
Средний химический состав базальта по P. Дэли (%): SiO2 — 4&,06; TiO2 — 1,36; Аl2O3 — 15,70; Fe2O3 — 5,38; FeO — 6,37; MgO — 6,17; CaO — 8,&5; Na2O — 3,11; K2O — 1,52; MnO — 0,31; P2O5 — 0,45; H2O — 1,62.
и из него успешно вату делают для теплоизоляции.
#9 aversun
Как бы базальт тоже силикат.
А кто же с этим спорит, только базальт — основная порода, по сути представляющая собой затвердевший (и часто афировый) расплав с температурой кристаллизации 900-950°С. Осадочные породы состоят из суммы отдельных минералов или фрагментов интрузивных пород. Песчаники (алевролиты, аргиллиты и т.д.) содержат часто немалую долю кварца и по этому достаточно тугоплавки. Глины тоже часто отличаются тугоплавкостью. По этому для каменного литья эти породы, как правило, не используются.
#10 TreeLoys
Может ли мрамор плавиться?
Известный «столешников9 впаривает своим посетителям, что горы Ирана, Турции и Греции, это «мрамор, расплавленный бомбардировкой ВКЦ- великой космической цивилизации
«.
Фотографии путешествий по Ирану, Турции и Греции там интересные, но вот, химиков там, похоже, нету.
Я тоже к химии отношусь уважительно издалека, но, вот, насчет «плавления мраморных гор» имеются большие сомнения.
Но многие вещи непонятно как сделаны, опустив за скобки плавление мрамора.
Литье из базальта и диабаза широко распространено в промышленности.
Причем это именно литье в прямом смысле слова, а не смесь каменного порошка с клеем, грубо говоря.
«Путем расплавления различных горных пород, последующей разливки расплава в формы и охлаждения получают строительные изделия, обладающие высокой химической стойкостью, прочностью и твердостью. В качестве сырья для изготовления, изделий каменного литья используют обычно горные породы магматического происхождения — диабазы и базальты. Эти породы по химическому составу достаточно постоянны и дают возможность получить изделия высокой плотности, стойкости в агрессивных средах и с повышенной сопротивляемостью истиранию. Изделия из диабазов и базальтов имеют темную окраску вследствие наличия в них темноокрашенных минералов. Для получения изделий каменного литья светлых тонов в качестве сырья используют кварцевый песок, доломит, мел и мрамор. Для снижения температуры плавления шихты и отбеливания состава расплава в шихту вводят плавиковый шпат и окись цинка.
Плавление диабаза и базальта чаще всего производится в ванных печах при температуре 1400-1500. С. Готовый расплав из ванной печи поступает в разливочный ковш (копильник) и охлаждается до температуры около 1250. С. Охлаждение расплава перед разливкой в формы необходимо для образования надлежащей структуры изделий и снижения усадочных деформаций. Затем расплав выливается в земляные или металлические формы или формы из силикатных материалов и постепенно охлаждается. При охлаждении каменного литья в формах внутри изделий возникают вредные напряжения, повышающие хрупкость. Для снижения внутренних напряжений и образования кристаллической структуры изделия подвергаются отжигу обычно в туннельных или камерных печах при температуре 800-900. С. После отжига готовые изделия поступают на склад.
Изделия каменного литья выпускают в виде плоских и изогнутых плиток, деталей желобов, труб, штуцеров и др. Поверхность изделий практически не поддается механической обработке вследствие высокой твердости. Водопоглощение незначительное. Термостойкость 150-200. С. Высокая химическая стойкость изделий каменного литья (кислостойкость 99-100%) позволяет с успехом использовать их на химических заводах для покрытия полов, устройства сливных каналов, в качестве футеровочного материала; высокая сопротивляемость истиранию дает возможность применять эти изделия для футеровки шаровых мельниц и других аппаратов, где возникают большие истирающие усилия.
И ли у «столешникова9 проблема с правильным определением минерала, потому что, если то, что он называет «мрамор9 вовсе не «мрамор9, а «гранит9- то он плавится, судя по реплике знатока на этом же форуме.
Не льют, а чаще выпекают. Так технологически проще.
Гранит достаточно разнороден и имеет разные температуры плавления своих составных частей.
Температура плавления гранита оценивается в пределах 950-1300 оС, что для современных технологических возможностей не много. Гранит поддается плавлению при относительно низких температурах, за исключением некоторых окислов тугоплавких элементов, входящих в его состав, что и определяет зернистую структуру гранита.
В приципе, можно и отлить в граните, если задаться такой целью.
По температурам ядерного взрыва и воздействию на камни
Во время легендарного взрыва «Ивана9 50 МТ (50 000 000 тонн тротил. экв.) испарялись камни.
Высоат «гриба9 — 64 км.
Радиус «активной зоны» (температура более миллиона гразусов) 4,5 км.
Разрушения от ударной волны — 400 км. от центра.
Световой импульс (воздействие) — 270 км.
От острова над которым был подорван заряд остался ровный «вылизанный9 каменный «каток9.
Это был самый стильный рукотворный взрыв.
А ведь тогда хотели взорвать не 50 МТ а все 100 МТ.
—
Восточно-Иранские горы сложены осадочными породами, гранитоидами и лавами
осадочные породы подразделяются на :
обломочные (терригенные) (см. песчаник, брекчия, алевролит)
хемогенные (см. боксит, латерит, каменная соль, доломит)
органогенные (см. коралловые известняки, диатомиты, торф, каменный уголь)
смешанные, например, вулканогенно-осадочные (см. вулканический туф)
Грани́т
(итал. granito. от лат. granum
— зерно) — магматическая глубинная горная порода кислого состава. нормального ряда щёлочности. Состоит из кварца. плагиоклаза. калиевого полевого шпата и слюд — биотита и/или мусковита. Граниты очень широко распространены в континентальной земной коре. Эффузивные аналоги гранитов — риолиты. Плотность гранита — 2600 кг/м³, прочность на сжатие до 300 МПа
Температура плавления 1215—1260 °C
;
при присутствии воды и давления температура плавления значительно снижается — до 650 °C
Основной тип лавы, извергаемый из мантии. характерен для океанических щитовых вулканов. Наполовину состоит из диоксида кремния. наполовину — из оксидов алюминия. железа. магния и других металлов.
Имеет высокую температуру (1200—1300 °C).
Для базальтовых лавовых потоков характерны малая толщина (метры) и большая протяжённость (десятки километров).
Цвет горячей лавы — жёлтый или жёлто-красный.
Наполовину состоит из карбонатов натрия и калия.
Это самая холодная и жидкая лава, она растекается подобно воде. Температура карбонатной лавы всего 510—600 °C.
Цвет горячей лавы — чёрный или тёмно-коричневый, однако по мере остывания становится светлее, а спустя несколько месяцев становится почти белым.
Застывшие карбонатные лавы — мягкие и ломкие, легко растворяются в воде.
Карбонатная лава течёт только из вулкана Олдоиньо-Ленгаи в Танзании.
Наиболее характерна для вулканов Тихоокеанского огненного кольца. Обычно очень вязкая и иногда застывает в жерле вулкана ещё до окончания извержения, тем самым прекращая его. Закупоренный пробкой вулкан может несколько вздуться, а затем извержение возобновляется, как правило, сильнейшим взрывом. Средняя скорость потока такой лавы — несколько метров в день, а температура — 800—900 °C. Она содержит 53-62 % диоксида кремния (кремнезёма). Если его содержание достигает 65 %, то лава становится очень вязкой и медленной. Цвет горячей лавы — тёмный или чёрно-красный. Застывшие кремниевые лавы могут образовать вулканическое стекло чёрного цвета. Подобное стекло получается, когда расплав быстро остывает, не успевая
Мрамор
(др.-греч. μά9rho;9mu;9alpha;9rho;9omicron;9sigmaf; — «белый или блестящий камень») — метаморфическая горная порода, состоящая только из кальцита CaCO3. При перекристаллизации доломита CaMg(CO3)2 образуются доломитовые мраморы.
Образование мрамора — результат так называемого процесса метаморфизма: под воздействием определённых физико-химических условий структура известняка (осадочная горная порода органического происхождения) меняется, и в итоге рождается мрамор.
В строительной практике «мрамором9raquo; называют метаморфические породы средней твёрдости, принимающие полировку (мрамор,
мраморизованный известняк. плотный доломит, карбонатные брекчии и карбонатные конгломераты).
О добыче мрамора в Иране- таки да, добывают:
Мы с удовольствием представляем нашу корпорацию «Omarani Yazdbaf» — это известная корпорация по добыче камня. Наша компания ведет добычу оникса (светло-зеленый, белый), мрамора (кремовый, оранжевый, красный, розовый, желтый) и травертина (шоколадный, коричневый
—
В общем, так ничего и непонятно- кто залез на гору и для чего выбил в горе рельеф.
Температура и особенности процесса плавления алмазов
Алмаз - драгоценный камень. но его свойства физики оценили по достоинству только в XVI веке. И это несмотря на то что камень был найден несколькими столетиями раньше. Конечно, чтоб оценить всю значимость минерала, потребовалось провести немало опытов. Они дали информацию о том, какая твердость у камня, температура плавления алмаза, а также другие физические характеристики. Но с тех пор камень используют не только в качестве красивого аксессуара, но еще и в промышленных целях.
Оценка проводилась в специальных лабораториях. И в результате был выяснен химический состав алмаза. строение его кристаллической решетки, а также открыто несколько феноменов.
Опыты, связанные с температурой плавления
Как известно, кристаллическая решетка вещества имеет форму тетраэдра с ковалентными связями между атомами углерода. Возможно, что именно такая структура стала причиной нескольких открытий, связанных с плавлением алмаза.
Энциклопедии минералов дают показатели плавления алмазов 3700-4000 градусов по Цельсию. Но это не совсем точная информация, поскольку они не поддаются общепринятым закономерностям. В частности, во время плавления были обнаружены такие эффекты:
- Используя высокие температуры (2000 градусов Цельсия без доступа кислорода), алмаз можно превратить в графит. При этом дальнейшее поведение этого вещества с повышением температуры не поддается логическому объяснению. А вот процесс в обратную сторону произвести невозможно. В крайнем случае можно получить синтетический камень, кристаллическая решетка которого будет отличаться от природных алмазов.
- Если же нагревать камень до температуры 850-1000 градусов по Цельсию, он превращается в углекислый газ, то есть исчезает без следа. Такой опыт провели в 1694 году исследователи из Италии Тарджони и Аверани, пытаясь расплавить камни и соединить их в один алмаз.
- Исследования проводились и в 2010 году в Калифорнии, где группа физиков сделала вывод, что добиться плавления алмаза невозможно, если постепенно повышать температуру камня. Чтоб выяснить показатель плавления, необходимо, кроме температуры, воздействовать на алмаз давлением, а это затрудняет измерение. Чтоб действительно перевести алмаз в жидкое состояние, ученым потребовалось приложить немало усилий. Для этого они использовали импульсы лазера, которые действовали на камень несколько наносекунд. При этом камень в жидком виде был получен при давлении, в 40 миллионов раз превосходящем атмосферное на уровне моря. Кроме того, если давление понижалось до 11 миллионов атмосфер, а температура при этом на поверхности минерала была 50 тысяч Кельвинов, то на камне появлялись твердые кусочки. Они не тонули в остальной жидкости и внешне напоминали кусочки льда. При дальнейшем понижении показателя давления, кусочки скапливались, образовывая «айсберги» на плаву. Ученые сопоставили, что так ведет себя углерод в составе планет Нептуна и Урана, на поверхности этих небесных тел тоже существуют океаны с жидким алмазом. Но чтоб доказать это предположение, необходимо отправить спутники к планетам, что на сегодняшний момент невозможно быстро осуществить.
- Если действовать на камень короткими световыми импульсами в ультрафиолетовом диапазоне, то в минерале появятся небольшие углубления. Таким образом эксперимент подтверждает исчезновение камня под действием мощного ультрафиолета, то есть превращения алмаза в углекислый газ. Поэтому ультрафиолетовые лазеры на основе алмаза быстро ломаются и становятся непригодными к использованию. Но не следует переживать по поводу того, что бриллиант на украшении исчезнет со временем: чтоб удалить один микрограмм минерала, придется держать алмаз под ультрафиолетом около 10 миллиардов лет.
Итак, показатель плавления - интересная характеристика алмаза. Она все еще является предметом для изучения. С появлением технологий ученые находят новые способы проверки этой характеристики. На ее основе можно сделать выводы по поводу происхождения камня, открыть новые способы применения алмаза.
Вот тебе и нынешнее воспитание, - назидательно произнес Янечек. - А если иной раз скажешь что-нибудь сыну, отвечает: «Вы, батя, этого не понимаете, теперь другие времена, другая эпоха… Ведь и костяное оружие, говорит, еще не последнее слово: когда-нибудь материал». Ну, знаешь ли, это уж слишком: разве видел кто материал крепче камня, дерева или кости! Ты хоть и глупая баба, а должна признать: что… что… ну, что это переходит все границы.
Карел Чапек. О падении нравов (из сб. «Апокрифы»)
Сейчас мы просто не в состоянии представить нашу жизнь без металлов. Мы привыкли к ним настолько, что по крайней мере подсознательно противимся - и в этом подобны процитированному выше герою доисторической эпохи - всяким попыткам заменить металлы чем-нибудь новым, более выгодным. Нам хорошо известно, с каким трудом в некоторых отраслях пробивают себе дорогу более легкие, более долговечные и более дешевые материалы. Привычка - это железный корсет, но и он, будь он из пластика, был бы все-таки более удобным. Впрочем, мы перескочили пару-другую тысячелетий. Первые потребители металла вообще не подозревали, что будущие поколения поставят их открытие в ряд с самыми выдающимися вехами на пути экономического и технического развития - с возникновением земледелия и с промышленной революцией XIX столетия.
Открытие, вероятно, состоялось - как это иногда случается - в результате какой-то неудачной операции. Ну, например, так: доисторическому земледельцу потребовалось пополнить запас каменных пластинок и топоров. Из кучи заготовок, лежавшим у его ног, он выбирал камень за камнем и умелым движениями отбивал одну пластину за другой. А потом в его руки попал какой-то блестящий угловатый камень, от которого, сколько он ни бил по нему, ни одна пластинка не отделялась. Более того, чем усерднее он дубасил по этому бесформенному куску сырья, тем больше тот начинал походить на лепешку, которую в конце концов можно было мять, крутить, вытягивать в длину и свивать в самые удивительные формы. Так люди впервые познакомились со свойствами цветных металлов - меди, золота, серебра, электрона. При изготовлении первых, очень простых украшений, оружия и инструментов им было достаточно самого распространенного технического приема каменного века - удара. Но эти предметы были мягкими, легко ломались и затуплялись. В таком виде они не могли угрожать господству камня. А кроме того, металлы в чистом виде, поддающиеся обработке камнем в холодном состоянии, в природе встречаются крайне редко. И все-таки новый камень им понравился, поэтому они экспериментировали с ним, комбинировали приемы обработки, ставили опыты, думали. Им пришлось, естественно, пережить много неудач, и прошло очень много времени, прежде чем им удалось открыть истину. При высокой температуре (ее последствия они хорошо знали по обжигу керамики) камень (который мы сегодня называем медью) превращался в текучее вещество, принимавшее вид любой формы. Инструменты могли обрести очень острую режущую кромку, которую к тому же можно было затачивать. Сломанный инструмент не надо было выбрасывать - достаточно было его расплавить и снова отлить в форме. Потом они пришли к открытию, что медь можно получать обжиганием различных руд, которые встречаются куда чаще и в большем объеме, нежели чистые металлы. Конечно, они не узнали с первого взгляда металл, скрытый в руде, но эти ископаемые, несомненно, привлекали их своей пестрой окраской. А когда к этому после длинного ряда случайных, а впоследствии сознательных количественных экспериментов прибавилось открытие бронзы - твердого золотистого сплава меди и олова, длившееся миллионы лет господство камня пошатнулось в само своем основании.
В Центральной Европе медные изделия впервые появились в единичных случаях на закате неолита, несколько чаще они встречались в энеолите. Однако уже раньше, в седьмом - пятом тысячелетиях до н. э., более развитый Ближний Восток начал получать медь плавкой пригодных для этой цели окисных (куприт), карбонатных (малахит), а позднее и сульфидный руд (медный колчедан). Самой простой была плавка окисных руд, полученных из выветрелых медных месторождений. Такие руды можно при температуре 700–800 град. восстановить в чистую медь:
Cu2 O + CO → 2Cu+CO2
Когда древние литейщики прибавили к этому продукту олово (вспомним о египетском рецепте), возник сплав, который по своим свойствам далеко превосходил медь. Уже полпроцента олова повышает твердость сплава в четыре раза, 10 процентов - в восемь раз. Одновременно снижается точка плавления бронзы, на пример при 13 процентах олова почти на 300 °C. Отрылись врата в новую эпоху! За ними мы уже не встретим то старое однородное общество, где каждый делал почти все. Изготовлению предмета из металла предшествовал долгий путь - поиски рудных месторождений, добыча руды, плавка в плавильных ямах либо печах, разливка в изложницы; все это требовало целого комплекса специальных знаний и навыков. Поэтому среди ремесленников начинается дифференциация по специальностям: горняки, металлурги, литейщики и, наконец, торговцы, род занятий которых необходим остальным и потому ими высоко ценится. Не каждый мог успешно заниматься всем комплексом столь сложной деятельности. Со многими неудачами и трудностями столкнулись и современные экспериментаторы, когда попытались повторить некоторые технологические приемы доисторических металлургов и литейщиков.
Сергей Семенов обнаружил трассологическим методом и экспериментально подтвердил тот факт, что на заре бронзовой эры люди использовали для добычи и дробления руд весьма грубые каменные орудия из гранита, диорита и диабаза в виде мотыг, дубинок, наковален и дробилок.
Плавку малахитовой руды экспериментаторы опробовали в небольшом углубленном горне без использования воздушного дутья. Горн они высушили и обложили каменными плитами таким образом, что возникла круглая амбразура с внутренним диаметром около одного метра. Из древесного угля, использовавшегося в качестве топлива, в горне сделали конусообразное сооружение, в середину которого положили руду. После нескольких часов горения, когда температура открытого пламени достигала 600–700 °C, малахит расплавился до состояния оксидической меди, то есть металлическая медь не образовалась. Аналогичный результат был достигнут и в следующей попытке, когда вместо малахита использовали куприт. Причина неуспеха заключалась, по всей вероятности, в избытке воздуха в горне. Новый тест с малахитом, накрытым перевернутым керамическим сосудом (весь процесс протекал так же, как и в предыдущих случаях), принес в итоге медь губчатого вида. Небольшое количество цельной меди экспериментаторы получили лишь тогда, когда малахитовую руду перед плавкой раздробили. Сходные опыты были проведены в Австрии, альпийские руды которой имели огромное значение для доисторической Европы. Однако в печь экспериментаторы нагнетали воздух, благодаря чему достигли температуры 1100 °C, которая восстанавливала окислы в металлическую медь.
В одном из опытов экспериментаторы использовали для отливки бронзового серпа сохранившуюся из находок у Цюрихского озера половину оригинальной каменной формы, к которой изготовили парную сторону. Обе части формы высушили при температуре 150 °C и лили бронзу при 1150 °C. Форма осталась неповрежденной, отливка была хорошая. Тогда решили опробовать уже бронзовую двухстворчатую форму для топора, найденную во Франции. Она была тщательно просушена при температуре 150 °C. Потом ее залили бронзой при температуре 1150 °C. Было получено изделие великолепного качества. При этом не было обнаружено ни малейшего повреждения на бронзовой форме, что стало самым важным результатом эксперимента. Дело в том, что перед экспериментом некоторые исследователи высказывали мнение, что горячий металл, по всей вероятности, соединится с материалом формы.
При производстве предметов более сложной конфигурации древние литейщики использовали технику литья с потерей литейной формы. Восковую модель они обмазывали глиной. При обжиге глины воск вытекал, и его потом замещала бронза. Однако, вынимая бронзовую отливку, формы приходилось разбивать, так что рассчитывать на ее вторичное использование не приходилось. Экспериментаторы отрабатывали этот метод, исходя из технологической инструкции XVI века по изготовлению золотых и серебряных бубенчиков. Во время опытов они заменили золото медью, чтобы одновременно проверить возможность замены драгоценных металлов обычными. Температура плавления золота равна 1063 °C, меди - 1083 °C. В качестве образца была выбрана отливка медного бубенчика из стоянки первого тысячелетия до н. э. Форму изготовили из смеси глины и древесного угля, а модель - из пчелиного воска. Малое ядро сделали из смеси глины и молотого древесного угля и поместили в него маленький камешек - сердце бубенчика. Воск нанесли вокруг ядра тонким слоем, равным толщине стенки будущей отливки, и прилепили восковое кольцо, образующее подвесок будущего бубенца. Восковую бобышку в форме рукоятки прикрепили над кольцом таким образом, чтобы она служила бункером для расплавленного металла во время разливки, затвердевания и усадки металла в отливке. В восковой оболочке на нижней части бубенца вырезали отверстие, чтобы формообразующая смесь из глины, древесного угля и воска заполнила отверстие и зафиксировала положение ядра после выплавки восковой модели и во время литья. Обернутую форму в верхней части проткнули несколькими соломинами, которые позже либо сгорели, либо просто были удалены. Через возникшие отверстия из формы во время литья выходил горячий воздух. Всю модель покрыли несколькими слоями размолотой глины и древесного угля и в течение двух дней сушили. Потом ее еще раз покрыли слоем угля и глины (для прочности формы) и над бобышкой прикрепили воронкообразный заливочный бункер из той же формообразующей смеси. Бобышку прикрепили слегка наискось, чтобы форма отливалась в наклонном состоянии. Это должно было обеспечить беспрепятственное стекание расплавленного метла по нижней части ее лицевой стороны, в то время как по противоположной стороне должен был происходить отток вытесняемого металлом воздуха до полного наполнения всей формы расплавленным металлом. Перед плавкой в бункер закрытый крышкой бросили обломки медной руды. После сушки форму поместили в печь, оборудованную каналом, обеспечивающим тягу. Печь заполнили четырьмя с половиной килограммами древесного угля и разогрели до температуры 1200 °C. Восковая модель и восковая бобышка расплавились и выпарились, медь расплавилась и стекла в форму, где и образовала металлический бубенчик. Потом внешнюю «рубашку» разбили, металлическую бобышку удалили, а глиняное ядро, образовавшее полую часть бубенца, выковыряли - остался только камешек.
Артур Питч провел целую серию экспериментов, посвященных чеканке бронзы: выделке проволоки, спирали, листа, сплошного кольца и профильного прута. Приобретенный опыт был использован им при изготовлении реплик бронзовых крученых колец дуринской культуры, относящейся к раннему железному веку. Всего сделал он семнадцать реплик, каждую из которых снабдил описанием археологического оригинала, перечнем использованных инструментов и приспособлений, анализом вещественного состава и, наконец, объяснением отдельных операций и указанием на длительность технологического процесса. Менее всего времени было затрачено на реплику номер два - двенадцать часов. Наибольшее - шестьдесят часов - потребовала реплика номер четырнадцать.
На протяжении бронзового века стали постепенно выявляться и неудобства, связанные с производством, прежде всего ограниченное наличие в природе сырьевых источников и истощение известных к тому времени месторождений. Это, безусловно, было одной из причин, почему люди искали новый металл, который мог бы удовлетворить постоянно возрастающие потребности. Этим требованиям отвечало железо. Сначала судьба его напоминала судьбу меди. Первое железо, метеоритного происхождения, либо полученное случайно, появилось уже в третьем и втором тысячелетиях до н. э. в Восточном Средиземноморье. Более трех тысячелетий назад стали работать металлургические печи в Передней Азии, Анатолии и Греции. У нас они появились в гальштатскую эпоху, но окончательно привились только в латенскую эпоху.
Среди сырья, применявшегося в древнем железоплавильном деле (окислы, карбонаты, силикаты). Наиболее распространенными были окислы: гематит, или железный блеск, лимонит, или бурый железняк, - смесь гидроокисей железа и с большим трудом восстанавливаемый магнетит.
Восстановление железа начинается уже приблизительно при температуре 500 °C. Вы, вероятно, сейчас зададите вопрос, почему железо стало применяться на столетия или тысячелетия позже меди и бронзы. Это объясняется условиями его тогдашнего производства. При тех температурах, которые достигались первыми металлургами в их горнах и печах (около 1100 °C), железо никогда не переходило в жидкое состояние (для этого необходимо хотя бы 1500 °C), а скапливалось в виде тестообразной массы, которая в благоприятных условиях сваривалась в крицу, пропитанную шлаком и остатками горючих материалов. При такой технологии в железо из древесного угля переходило ничтожно малое количество углерода - около одного процента, поэтому оно было мягким и поддающимся ковке даже в холодном состоянии. Изделия из такого железа не достигали твердости бронзы. Острия легко загибались и быстро затуплялись. Это было так называемое прямое, непосредственное производство железа. Оно сохранялось вплоть до XVII столетия. Правда, в некоторых доисторических и раннесредневековых печах можно было получить железо с более высоким уровнем углеродистости, то есть некое подобие стали. Только с XVII столетия стали применяться печи, где железо производилось в жидком состоянии и с высоким содержанием углерода, то есть твердое и хрупкое, из которого отливался слиток. Для получения стали необходимо было высокоуглеродистому железу придать ковкость путем удаления части содержащегося углерода. Поэтому такой метод называется непрямым производством железа. Но и доисторические кузнецы путем экспериментов расширяли свой опыт. Они обнаружили, что, нагревая железо в кузнечном горне, когда температура от древесного угля достигнет 800–900 °C, можно получать изделия с гораздо лучшими свойствами. Дело в том, что на их поверхности образуется тонкий слой с более высоким содержанием углерода, который придает предмету качества низкоуглеродной стали. Твердость железа возросла, когда был открыт принцип закалки и стали использоваться его преимущества.
Вероятно, самый ранний эксперимент в изучении древней металлургии распорядился провести около ста лет назад граф Вурмбранд. Его рабочие-металлурги в простейшем горне диаметром полтора метра использовали древесный уголь, обожженную руду и в процессе плавки улучшали условия горения слабым нагнетанием воздуха. Через двадцать шесть часов они получили приблизительно двадцатипроцентный выход железа, из которого выковали различные предметы. Сравнительно недавно плавку железной руды в аналогичном устройстве провели и английские экспериментаторы. Простой плавильный горн они реконструировали по подобию горна, обнаруженного на одной древнеримской стоянке. Оригинальный горн имел диаметр 120 см и глубину 45 см. Перед плавкой английские исследователи обожгли руду в окислительной среде при температуре 800 °C. После зажигания древесного угля в горн постепенно добавляли новые слои руды и древесного угля. В ходе эксперимента было использовано искусственное дутье фурмой. Для того, чтобы один слой руды, восстановленный окисью углерода, проник в под, требовалось около четырех часов. Рабочая температура доходила до 1100 °C, и железо скапливалось около устья фурмы. Выход в процессе плавки составил 20 процентов. Из 1,8 кг руды было получено 0,34 кг железа.
Опыты Гиллеса в 1957 году открыли серию экспериментов, посвященных восстановлению руды в различных типах шахтных печей. Уже в первых опытах Иозеф Вильгельм Гиллес доказал, что доисторическая печь шахтной конструкции могла успешно работать, используя естественное движение воздуха на подветренных склонах. Во время одного из тестов он зафиксировал в центре печи температуру от 1280 до 1420 °C, а в пространстве колосника - 250 °C. Результат плавок - 17,4 кг железа, то есть 11,5 процента: шихта состояла из 152 кг бурого железняка и железного блеска и 207 кг древесного угля.
Множество опытных плавок в репликах печей римской эпохи провели в Дании, особенно в Лейре. Выяснилось, что одна удачная плавка может дать 15 кг железа. Для этого датчане должны были использовать 132 кг болотной руды и 150 кг древесного угля, который получили жжением одного куб. м древесины лиственных пород. Плавка продолжалась около 24 часов.
Систематические эксперименты проводятся в Польше в связи с изучением обширного железоделательного ареала, открытого в Свентокшиских горах. Его расцвет относится к поздней римской эпохе (от третьего до четвертого столетия н. э.). Только с 1955 по 1966 год археологи исследовали в Свентокшиских горах 95 металлургических комплексов с более чем 4 тысячами железоплавильных печей. Археолог Казмеж Беленин полагает, что общее число таких комплексов в этом ареале составляет 4 тысячи с 300 тысячами печей. Объем их продукции мог достигать 4 тысяч тонн железа рыночного качества. Это огромная цифра, не имеющая аналогов в доисторическом мире.
Истоки упомянутого железоплавильного производства восходят к позднему латену (последнее столетие до н. э.) и раннему римскому периоду, когда металлургические комплексы с десятью или двадцатью печами располагались непосредственно в центре населенного пункта. Их продукция удовлетворяла лишь местные, весьма ограниченные потребности. Начиная со среднего римского период производство железа стало носить организованный характер, наибольшего подъема оно достигла в III–IV веках. Печи располагались в виде двух прямоугольных отсеков, разделенных штреком для обслуживающего персонала. В каждом из отсеков печи группировались по две, три и даже по четыре. Таким образом, в одном комплексе размещалось несколько десятков печей, однако не были какими-то редкими исключениями и поселения с сотней и даже двумя сотнями печей. Гипотеза о существовании в этот период экспорта железа подтверждена не только количеством металлургических печей с высокой продуктивностью, но и многочисленными находками кладов с тысячами римских монет. В эпоху Великого переселения народов и в раннем средневековье производство снова упало до уровня, отвечавшего местным потребностям.
Предпосылкой возникновения столь массового металлургического производства в римскую эпоху стали достаточные запасы дерева и руды. Металлурги использовали бурый железняк, гематит, а также железный шпат. Некоторые руды они добывали обычным горняцким способом, о чем свидетельствует, например, шахта Сташиц с системой шахтных стволов, штолен и с остатками крепи и инструментов, относящихся к римской эпохе. Впрочем, не гнушались они и болотной рудой. Применялись печи с углубленным подом и надземным стволом, который при выемке железной губки (крицы) приходилось разбивать.
Начиная с 1956 года в Свентокшиских горах проводят эксперименты, которые реконструируют производственный процесс: добычу руды на кострах (для удаления влаги, обогащения и частичного сжигания вредных примесей, например серы); получение древесного угля углежжением в штабелях; строительство печи и сушку ее стен; разжигание печи и непосредственную плавку; разработку ствола шахты и выемку железной кубки; проковку железной кубки.
В 1960 году на одной из самых известных стоянок (Нова Сбупя) был открыт Музей древней металлургии, неподалеку от которого ежегодно, начиная с 1967 года, в сентябре демонстрируется для широкой публики технология доисторической металлургии. Такая демонстрация начинается с доставки руды из шахты в металлургический комплекс, в котором на разных уровнях размещены железоплавильные печи. Здесь руда размельчается молотами и сушится. Сушка и обогащение руды происходят в обжиговых сооружениях. Такое устройство имеет форму штабеля, образуемого слоями дров, переложенными рудой. Штабель поджигается одновременно со всех сторон. После сгорания высушенную, обожженную и обогащенную руду складывают в кучу, откуда ее берут для загрузки. В окрестностях комплекса находится также рабочее место угольщиков, где показывается производство древесного угля - закладка и возведение штабеля, выжигание, разборка штабеля, транспортировка угля на открытый склад, измельчение и, наконец, использование в печи. Затем следует разогрев печи, монтаж и закладка мехов. Персонал комплекса составляют десять работников - шахтеров, металлургов, угольщиков и подсобных рабочих, которые ведут плавку и одновременно готовят к эксперименту вторую печь. Плавка продолжается выемкой железной губки из пода, причем предварительно шахту не обходимо разбить.
В 1960 году польские и чешские специалисты объединили свои усилия и стали совместно проводить металлургические эксперименты. Они построили две восстановительные печи по образцам римской эпохи. Одна была аналогом типа печи из Свентокшиских гор, вторая соответствовала археологической находке в Лоденицах (Чехия). Для плавки были использованы гематитовая руда и буковый уголь в пропорции один к полутора и один к одному и слабое воздушное дутье. Систематически контролировали и измеряли приток воздуха, температуру и восстановительные газы. Во время эксперимента на аналоге польской печи, которая имела углубленный под и разные шахтные надстройки - высотой в 13, 27 и 43 см, ученые обнаружили, что плавильный процесс сосредоточился у горловин обеих противоположных фурм, где образовались подвижный шлак и губчатое железо (от 13 до 23 процентнов железа и лишь около одного процета металлического железа в каплях в составе нижнего шлака). Температура вблизи фурм достигала 1220–1240 °C.
Подобным же образом процесс протекал и во время опытов в лоденицкой печи; лиш9ь вид шлаковых и железных образований был иной. Температура вблизи фурмы составляла 1360 °C. И в этой реплике была получена железная крица со следами науглероживания. Железная кубка образовывалась всегда у горловин фурм, в то время как более легкий шлак протекал сквозь ее поры в под на слой древесного угля. Эффективность в обоих случаях не превышала 17–20 процентов.
Дальнейшие опыты были нацелены на выяснение уровня славянского металлургического производства VIII столетия, остатки которого сохранились в комплексах, открытых в Желеховицах у Уничова в Моравии. Речь шла прежде всего о том, чтобы определить, можно ли было в таких печах изготавливать сталь. Что касается выхода железа и эффективности печи, то это представляло второстепенный интерес, ибо проводившиеся в ходе эксперимента многочисленные измерения неблагоприятно влияли на процесс плавки.
Печи желеховицкого типа - замечательные устройства остроумной конструкции. Их форма позволяла проводить качественное наполнение завалкой. Опыты показали, что металлурги при плавке могли изготовлять древесный уголь сами. Топливо нужно было закладывать в печь малыми порциями, в противном случае появлялась опасность заблокировать узкое шахтное отверстие вплотную над подом печи. Бесспорным преимуществом обладали легкоплавкие железные руды, но печи желеховицкого типа были в состоянии восстанавливать и гематиты, и магнетиты. Предварительный обжиг руды не представлял сложности и был, по всей вероятности, в любом случае выгодным. Сантиметровый размер кусков руды был оптимальным.
Завалка образовывала плавящийся конус в поду печи, и засыпавшийся следом материал потом автоматически транспортировался к полости за фурмой, где образовывался эпицентр жала в котором продукт предохранялся от реоксидирования нагнетаемым воздухом.
Важным параметром является объем нагнетаемого в печь воздуха. Если дутье недостаточно, температура слишком низкая. Больший объем воздуха ведет к значительной потере железа, переходящего в шлак. Оптимальный объем вдуваемого воздуха, составлял для желеховицкой печи 250–280 л в минуту.
Далее экспериментаторы обнаружили, что при определенных условиях можно даже в примитивных отдельных печах получить высокоуглеродистую сталь и, следовательно, нет нужды в последующем науглероживании. Во время опытов на желеховицком комплексе археологи отметили тот факт, что все печи снабжены за фурмой раковиной. Это пространство они гипотетически приняли за камеру для нагревания и науглероживания крицы, которая там накапливалась сразу после плавки. Высказанную гипотезу они проверили в реплике желеховицкой печи. После шестичасовой плавки гематитовой руды с угля крицу нагрели в восстановительной среде в задней полости печи. Температура в камере составила 1300 °C. Продукт извлекли из печи при красно-белом калении. Шлак протекал через поры губчатой железной массы. Продукт содержал наряду с чистым железом железо науглероженное.
Во время новгородской археологической экспедиции в 1961 и 1962 годах были проведены экспериментальные плавки железа в реплике древнерусской надземной шахтовой печи X–XIII веков, хорошо известной как по археологическим, так и по этнографическим источникам. Учитывая то обстоятельство, что просушка печи из глины - а именно из нее были сделаны оригиналы - затянулась бы на несколько недель, экспериментаторы использовали при ее изготовлении сырье глиняные блоки. Зазоры между ними заполнили смазкой из глины и песка. Внутренность печей обмазали приблизительно сантиметровым слоем глины с песком. Печь имела цилиндрическую форму диаметром 105 см и высотой 80 см. Шестидесятисантиметровая домница была размещена в центре, цилиндра. Диаметр верхнего отверстия составлял 20 см, пода - 30 см. В нижней части печи экспериментаторы сделали отверстие размером 25х20 см, которое служило для нагнетания воздуха и выпуска шлака. Контроль за режимом внутри печи проводился через два диоптера в стенке, через которые были введены части измерительной аппаратуры. Дутье проводили новейшим способом - электромотором, мощность которого привели в соответствие с параметрами, достигавшимися кузнечными мехами. Двадцатисантиметровая фурма была опять репликой старого типа, изготовленной из смеси глины и песка. Пе6чь сохла три дня при нормальных погодных условиях.
Для плавок использовали по большей части болотную руду с весьма высоким содержанием железа (около 77 процентов), а в двух случаях и гипергенную руду, которую дробили до величины грецкого ореха. Перед завалкой руду высушили, а часть даже около получаса обжигали на огне. Плавка началась с разогрева печи сухими сосновыми поленьями с естественной тягой в течение двух часов. Потом домницу вычистили и под покрыли тонким слоем угольной пыли и колотого угля. Затем последовала установка фурмы и обмазка всех щелей глиной. Дутье начали, когда шахта была полностью заполнена через дымовое отверстие древесным углем. Спустя пять - десять минут сосновый уголь разгорелся, и через полчаса треть его сгорела. Пустое пространство, образовавшееся в верхней части шахты, было заполнено шихтой, состоявшей из угля и руды. Когда шихта осела, в образовавшуюся пустоту добавили еще порцию. Всего было проведено семнадцать опытных плавок.
Из завалки, состоявшей из 7 кг руды и 6 кг древесного угля, получили 1,4 кг губчатого железа (20 процентов) и 2,55 кг шлака (36,5 процентов). Масса древесного угля ни в одной из плавок не превышала массы руды. Плавки, проведенные при повышенных температурах, давали меньший объем железа. Дело в том, что при более высоких температурах в шлак переходило большее количество железа. Серьезное влияние на качество и эффективность плавки оказывала помимо температурного режима точность выбора оптимального момента для выпуска шлака. При слишком раннем либо, наоборот, слишком позднем выпуске шлак поглощал окислы железа, и это вело к меньшему объему выхода продукции. При высоком содержании окислов железа шлак становился вязким и поэтому хуже вытекал и отделался от губчатого железа.
Значение новгородских экспериментов особенно велико потому, что во время некоторых из них удалось выпустить шлак. Плавка длилась от 90 до 120 минут. В этом типе печи можно было за один цикл обработать до 25 кг руды и получить более 5 кг железа. Восстановленное губчатое железо осаждалось не непосредственно на дне печи, а несколько выше. Получение металлического чугуна из этого продукта представляло собой дальнейшую самостоятельную и сложную операцию, связанную с новым нагревом. И эти эксперименты подтвердили гипотезу о том, что и в обычных восстановительных печах при определенных условиях происходит науглероживание железа, то есть получается сырьевая сталь. В восстановительных печах, где процесс протекал без выпуска шлака, был получен конгломерат, которые состоял из губчатого железа (верхней части), шлака (в нижней части) и остатков угля. Отделение губчатого железа от шлака обыкновенно проводилось механическим способом.
В последнее время археологи обнаружили в Моравском Красе, в районе города Бланско, множество следов древней металлургической деятельности - поды печей, обломки, стен, фурм, кусковую породу, - датируемых X столетием. В модели одной из печей с карманообразным подом был проведен эксперимент, который показал, что в таком устройстве также могла производиться науглероженная стал и что губчатое железо спекается на уровне фурмы, и потому его невозможно обнаружить под шлаковыми слитками.
Интересное
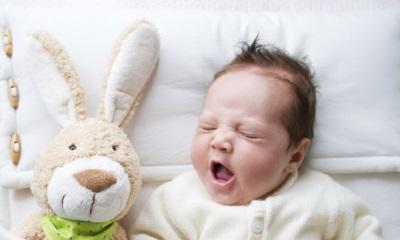
Как развивается двухмесячный младенец Медицинские препараты для лечения насморка у двухмесячного ребенка
Юмор
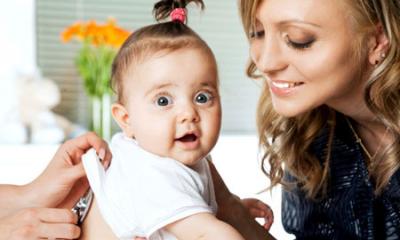
Что делать, если у ребенка высокая температура — инструкция для родителей
Рецепты
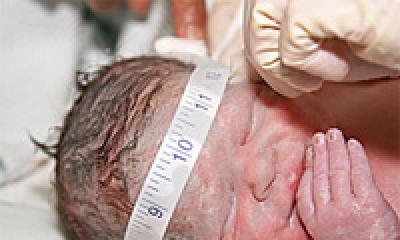